Since 2022, Oxess Snowsports has been collaborating with the Ithaka Institute for Carbon Strategies to enhance the physical properties of its snowboards through the use of the patented NanoCarbon injection technology. The NanoCarbon is derived from CO2 originally captured from the atmosphere by plants. The plant-based carbon is then converted into a highly persistent aromatic carbon through a technical process known as pyrolysis. When milled to nanometer-sized particles - a million times smaller than a millimeter - the resulting NanoCarbon powder can be injected into glass and carbon fibers to build snowboards and skis.
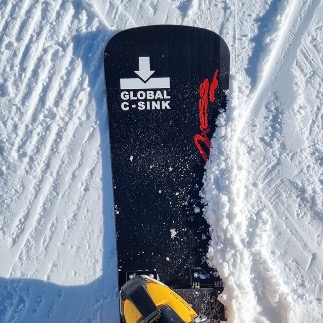
The injection of NanoCarbon reduces vibrations of the snowboard. However, its main and most significant effect is the enhancement of the rebound dynamics during turns. This improvement allows the snowboard to carve more easily through challenging conditions, ensures a more controlled rebound, and it significantly increases the speed as the board is pushed at the end of each turn.
As the carbon utilized in the snowboards is extracted from the atmosphere, each board acts as a carbon sink, representing a small but meaningful action against climate change. Consequently, all Oxess snowboards manufactured using this new nano-carbon technology are branded with the “Global C-Sink” label. Furthermore, snowboards adorned with the Global C-Sink label are climate-neutral, as all greenhouse gas emissions generated during their production have been offset by Carbon Standards through persistent carbon sinks.
Some more detailed background information about NanoCarbon and biochar technologies
Biochar is a porous, carbonaceous material produced from plant biomass and is considered one of the key materials for climate change mitigation. Today, biochar is mainly used in agronomy as a carrier of organic nutrients to increase crop yields or as an animal feed additive to improve animal health. However, specific biochar can also be used as a cement additive to improve concrete properties, as filler in plastics or advanced composite materials using epoxy resins.
When plants grow, they take-up CO2 from the atmosphere and transform it into biomass carbon. However, the carbon contained in biomass is not very stable, and it will, at the end of a plant’s lifecycle, decompose relatively quickly, releasing the carbon back into the atmosphere in the form of CO2. If, on the other hand, the biomass is pyrolyzed (heated under the absence of air to temperatures above 600°C), the carbon is transformed into a very stable form that can hardly be decomposed by microbes and will persist in the environment for many centuries as a carbon sink. Biochar was, therefore, acknowledged by the IPCC as one of only six key technologies to reverse climate change through negative emissions.
Using biochar in buildings or consumer products preserves the carbon initially extracted from the atmosphere by plants. As long as they are not combusted, biochar-containing products can be considered and certified as carbon sinks for climate mitigation. Using biochar in composite materials does, therefore, improve the product’s climate balance.
More detailed information about biochar can be found in the Biochar Journal (https://www.biochar-journal.org/en/biochar_society).
The biochar potential for being used in snowboards
Besides the carbon persistence that makes biochar a critical material to mitigate climate change, it was also shown that several of its properties could improve the quality of composite materials.
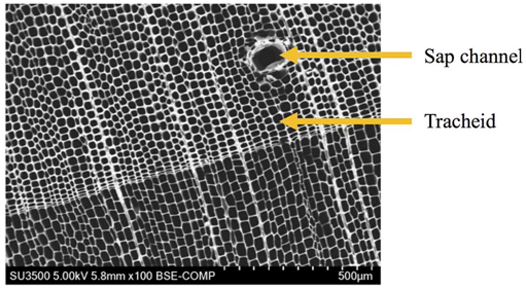
Biochar is a very porous material (like honeycomb). It contains more void than aromatic carbon matrices, as shown in the picture below, which shows, 500 times magnified, a biochar piece made from pine wood.
While the voids (containing non-moving air) are insulators, the carbonaceous walls are extremely strong (more than carbon fiber). At about 200 g / l, the material is very light.
Adding micronized biochar to epoxy resin for laminating glass- and carbon fiber lets us expect the following improvements when used in snowboards and similar high-performance materials
- Reduced vibration
- Increased damping and rebound
- Improved flexural, compressive, and tensile strength
- Gain in weight using less epoxy
- Better resin distribution and fibre fabric penetration
- Increased heat/cold buffering (intense heating of the ski, fins, foils at high speeds)
- Reduced electro-static charging
- Reduced cracking
- Improved adhesion between titanal, rubber, glass, and/or wood core
- Reduced softening and aging of the composite material
.